In a world where operational efficiency and asset reliability define competitive advantage, Enterprise Asset Management (EAM) systems are no longer optional—they’re essential. But simply adopting an EAM solution is not enough. The true challenge lies in maximizing the value it brings to your organization. From improving asset performance to reducing downtime and enhancing compliance, the returns on a well-implemented EAM platform can be transformative. However, that value is only realized when EAM is fully integrated into your culture, technology stack, and strategic planning.
This comprehensive guide explores the practical strategies organizations can adopt to maximize EAM value across multiple levels. We will explore the distinctions between EAM and related systems, discuss implementation pillars, examine multisite rollouts, and offer a roadmap to ROI. Whether you’re deploying an EAM platform for the first time or looking to enhance an existing one, this guide will help you extract long-term benefits.
Understanding EAM and Its Role in Asset-Intensive Industries
Enterprise Asset Management (EAM) software enables organizations to manage the full lifecycle of physical assets—from acquisition and operation to maintenance and disposal. It’s particularly crucial for sectors such as manufacturing, energy, transportation, and utilities, where asset reliability directly impacts profitability.
At its core, EAM helps schedule maintenance, track work orders, manage spare parts, and ensure compliance. However, EAM’s value extends far beyond basic maintenance tracking. It allows for strategic asset planning, supports sustainability goals, and improves financial forecasting. When implemented correctly, it serves as the foundation of a data-driven asset management strategy.
Key Differences Between EAM, CMMS, IM, and APM
It’s common to confuse EAM with other asset-related systems like CMMS (Computerized Maintenance Management Systems), IM (Integrity Management), and APM (Asset Performance Management). While each system plays a role in asset optimization, they serve different purposes and should be used in tandem.
Software | Key Focus | Primary Users | Core Benefits |
---|---|---|---|
EAM (Enterprise Asset Management) | Managing the full asset lifecycle | Maintenance teams, operations managers | Work order management, asset tracking, lifecycle visibility |
CMMS (Computerized Maintenance Management System) | Daily maintenance execution | Maintenance technicians, supervisors | Efficient task scheduling, real-time updates, maintenance records |
IM (Integrity Management) | Ensuring asset safety and compliance | Inspection teams, integrity engineers | Regulatory compliance, risk reduction, operational integrity |
APM (Asset Performance Management) | Data-driven asset optimization | Reliability engineers, plant managers | Predictive maintenance, failure forecasting, performance analytics |
Understanding how these systems intersect is crucial. For instance, an issue detected in IM can generate a work order in EAM, while APM uses data trends from EAM to prevent future failures.
The Foundation: Planning and Phased Implementation
One of the biggest mistakes organizations make is attempting an all-at-once rollout. To maximize EAM value, it’s better to start small and scale smart. A pilot implementation—targeting one location or asset group—allows teams to refine processes, gain early wins, and troubleshoot before full deployment.
A typical phased implementation includes the following steps:
- Preparation: Assess organizational readiness and gather cross-functional input.
- Initiation: Define KPIs and select initial sites or departments.
- Deployment: Configure the system to match workflows, integrate with ERP, and other tools.
- Go-Live: Roll out the platform with on-site support and informal coaching.
- Stabilization: Provide ongoing assistance, gather user feedback, and iterate.
This approach helps manage risk and allows the organization to learn iteratively, reducing resistance and improving long-term adoption.
The Role of Leadership in Driving Adoption
Maximizing the value of an EAM platform requires more than IT involvement. Leadership buy-in is essential for cultural and operational transformation. Executives must go beyond signing off on budgets—they need to become visible champions of the initiative.
Department managers, especially those in maintenance, operations, and engineering, play a crucial middle role. Their daily interaction with front-line teams makes them effective liaisons between strategic goals and tactical execution. When these managers endorse the EAM solution, adoption among their teams accelerates.
Moreover, identifying internal champions—natural influencers within teams—can help foster peer-led support networks. These early adopters reduce fear of change, promote best practices, and assist in training their colleagues.
EAM Integration: The Secret to Unlocking Value
Interoperability is non-negotiable. A standalone EAM system that doesn’t sync with your ERP, SCADA, or IoT platforms won’t deliver full value. Integrating systems enables a single source of truth for asset data, eliminating silos and supporting real-time decision-making.
When selecting an EAM system, look for open architecture, robust API support, and built-in connectors to common enterprise tools. Ensure the solution integrates seamlessly with financial systems, compliance reporting software, and production management tools.
Integration doesn’t just improve workflows—it also empowers predictive insights. Data from IoT sensors can feed into APM platforms, which then trigger work orders in EAM when thresholds are breached. This creates a proactive rather than reactive maintenance environment.
Customization and Flexibility for Different User Roles
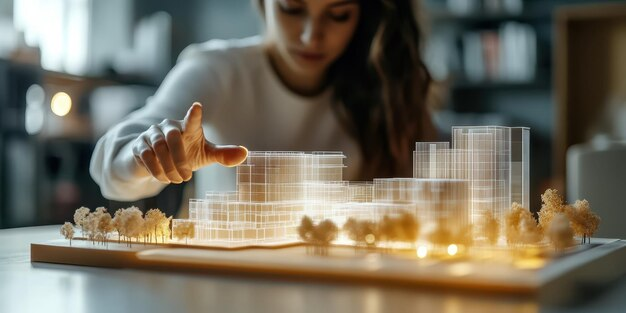
One size doesn’t fit all in asset management. Operators, technicians, supervisors, and managers each have different responsibilities, and your EAM platform should reflect that.
Modern systems offer role-based dashboards, personalized notifications, and customizable workflows. By tailoring the user experience, you reduce training time and boost productivity. Additionally, offline mobile access ensures field teams can stay productive even without connectivity, keeping asset data accurate and timely.
This level of configurability makes it easier to embed EAM into daily routines, rather than treating it as a separate system. And when users feel the system is built for them—not imposed on them—engagement rises.
Continuous Learning with Embedded Training Tools
Initial training is not enough. To maintain long-term value, organizations must invest in continuous learning. Today’s leading EAM platforms often include embedded e-learning tools that allow users to explore advanced features, refresh their knowledge, or onboard new team members independently.
Self-service modules reduce reliance on external training, promote self-sufficiency, and ensure standardized usage across multisite operations. They also allow teams to adapt quickly to system upgrades or new features, extending the lifecycle of your EAM investment.
Measuring Success: KPIs That Matter
Tracking the impact of EAM goes beyond uptime reports. To gauge real value, organizations must monitor a combination of operational, financial, and strategic metrics.
Key EAM performance indicators include:
- Overall Equipment Effectiveness (OEE): Tracks availability, performance, and quality.
- Planned Maintenance Percentage (PMP): Ratio of planned vs. reactive maintenance.
- Mean Time Between Failures (MTBF): Measures equipment reliability.
- Asset Uptime: Percentage of time assets are operational.
- Work Order Completion Rate: Indicates team efficiency and system usage.
These metrics reveal whether your EAM platform is improving operations or merely tracking them. They also support data-driven conversations with stakeholders about ROI.
Real-World Case: From Paper-Based to Predictive
Consider the example of Titan America, a major building materials manufacturer. By replacing legacy maintenance methods with a CMMS integrated into an EAM ecosystem, they reduced unplanned maintenance by 30%. Early wins built confidence among plant teams and laid the groundwork for wider EAM implementation.
The system’s integration with ERP software enabled real-time cost tracking, while predictive tools highlighted trends in equipment failure. Field technicians accessed job data offline via tablets, increasing field productivity and data accuracy. Titan’s experience proves that maximizing EAM value is not a one-time project—it’s a strategic evolution.
Conclusion
Maximizing EAM value is about more than software. It’s a combination of strategic planning, cultural buy-in, technical integration, and continuous improvement. When implemented correctly, EAM becomes a force multiplier—improving asset reliability, reducing costs, enhancing compliance, and enabling data-driven decisions.
To make the most of your investment, align EAM with organizational goals, empower your people through training, and ensure cross-platform compatibility. Remember that success is not measured by system go-live dates, but by how deeply EAM becomes embedded in your daily operations.
The companies that win in today’s asset-intensive environments are not the ones with the most data—they’re the ones who know how to use it. By maximizing EAM value, you ensure your organization is not only running efficiently today but is also future-proofed for tomorrow.
Iota Valley: A Fusion of Innovation and Nature
FAQs
What is the difference between CMMS and EAM in terms of functionality and scope?
CMMS focuses on maintenance task execution while EAM covers the full lifecycle of assets, including financial planning and strategic management
Why is user adoption critical for maximizing EAM value?
Without user engagement, even the most powerful EAM tools will remain underutilized,leadingg to poor data quality and missed opportunities
How does integrating EAM with ERP and IoT systems increase ROI?
Integration ensures a seamless data flow, enabling better decision-making, predictive maintenance, and reduced downtime across all operational areas..
What role do mobile and offline features play in field team efficiency?
They empower workers to log data access information and complete tasks in real tim,, even in remote areas, keeping asset records accurate and up.. ..o date
Can EAM help in regulatory compliance?
Y, by maintaining accurate records, scheduling timely inspections, and integrating with integrity management systems, EAM helps organizations meet compliance requirements efficiently.